Die Herstellung
von Leiterplatten
- Der Aufbau einer Platine oder Leiterplatte
- Die Leiterplattenherstellung Schritt für Schritt
- Die Entstehung der Struktur auf den Schichten der Leiterplatten
- Die Bestückung der Leiterplatten
- Die Fertigstellung der Leiterplatten bzw. die Bestückung im SMD-Verfahren
Leiterplatte, Platine oder Printed Circuit Board (PCB), es gibt ein paar Namen für diese wichtigsten Elemente moderner Geräte. Auf den Leiterplatten werden komplexe Schaltungen und Abläufe realisiert. Bei der Maicon Steuerungstechnik GmbH bildet die Entwicklung und Herstellung einen zentralen Baustein unseres Unternehmens. Wir hatten in anderen Blogbeiträgen ja schon über die Arten von Leiterplatten und die Entflechtung von Leiterplatten berichtet. Von daher wollen wir hier nur kurz darauf eingehen, um was es sich bei den Leiterplatten eigentlich handelt, damit wir uns dann ganz auf den Ablauf der Herstellung konzentrieren können.
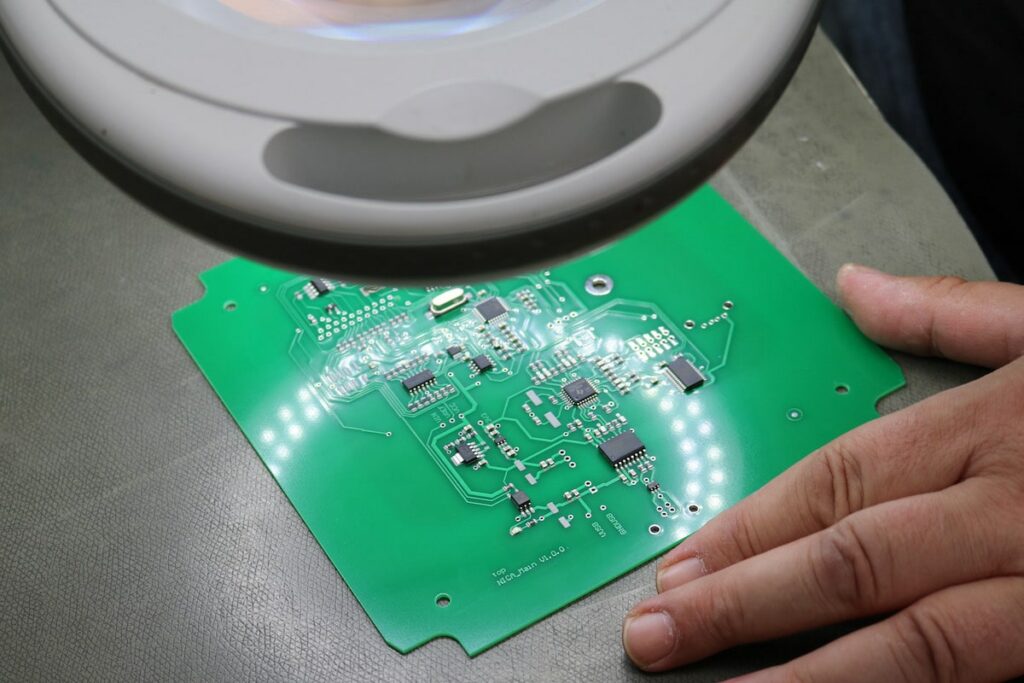
Der Aufbau einer Platine oder Leiterplatte
Der englische Begriff Printed Circuit Board (PCB) verrät es schon. Eine Leiterplatte oder Platine ist eine Art Karte, auf die Schaltkreise gedruckt und benötigte Bauelemente gelötet oder geklebt werden. Dabei werden auf modernen Leiterplatten beidseitig gleich mehrere Lagen von Schaltkreisen realisiert, um mehr Schaltkreise auf engstem Raum unterzubringen.
Damit der Strom auf dem PCB auch wirklich nur durch die jeweils angesteuerten Schaltkreise fließt, sind die verschiedenen Lagen und Kreise voneinander isoliert. Die geplanten Verbindungen zwischen den Schaltkreisen werden durch spezielle Kontaktierungen und Bohrungen zwischen den Lagen hergestellt. Das nichtleitende Grundmaterial, also das Substrat der Leiterplatten, besteht z.B. aus Epoxidharz oder auch aus günstiger Hartpappe, während die leitenden Elemente aus Kupfer bestehen.
Für viele kleinere Geräte wie Smartphones oder Kameras werden biegsame Leiterplatten benötigt. Diese werden dann aus einem entsprechenden Hochleistungskunststoff aus der Gruppe der Polyimide hergestellt, der nicht nur biegsam, sondern auch temperatur- und witterungsresistent ist.
Multilayer-Leiterplatten
Der Drang zur Miniaturisierung hat zur Entwicklung von PCB mit 16 oder sogar 48 Schichten bzw. Layer geführt. Diese extreme Komplexität an Schaltungen kann natürlich nur mit hochentwickelten Computerprogrammen beherrscht werden.
Grob zusammengefasst werden alle Schaltkreise auf der Leiterplatte oder dem einzelnen Layer platziert. Das CAE-Programm setzt dann bei der sogenannten Leiterplattenentflechtung den Entwurf des Schaltplans in ein kreuzungsfreies Leiterbahn-Netzwerk um und die notwendigen Unterbrechungen werden durch Wegätzen der Verbindungen erzeugt.
Im nächsten Abschnitt gehen wir auf die verschiedenen Schritte bei der Herstellung der Leiterplatten im Einzelnen ein. Dabei handelt es sich um eine verkürzte verallgemeinerte Beschreibung, die von Auftrag zu Auftrag und Art und Anforderungen an die Platinen anders aussehen mag.
Gerne beraten wir sie für eine individuelle Lösung
Die Leiterplattenherstellung Schritt für Schritt
Natürlich werden Leiterplatten in riesigen Stückzahlen in der Elektroindustrie hergestellt. Radios, Fernseher, Smartphones, Autos und viele weitere Massenprodukte können ohne PCB nicht funktionieren. Ein Dienstleister aus dem Mittelstand wie die Maicon Steuerungstechnik übernimmt dagegen die Herstellung von Leiterplatten, die in geringeren Stückzahlen oder für Einzelanfertigungen benötigt werden.
Dazu werden die Anforderungen an die Leiterplatte in mehr oder weniger elaborierter Form in Daten vom Auftraggeber an den Hersteller übermittelt. Häufig liegen die Daten bereits als sogenannte Gerber-Dateien vor, in denen viele Spezifikationen enthalten sind. Darin sind alle Details aus der Leiterplattenentflechtung enthalten wie das kreuzungsfreie Schaltungs-Netzwerk, die Breite der Leiterbahnen, die Größe und Platzierung der Bohrlöcher zwischen den Schichten, der Abstand zum Rand der Leiterplatte und vieles mehr.
Jedoch muss vor jedem jetzt zu planenden Schritt zunächst eine Machbarkeitsprüfung erfolgen. Erst diese sogenannte Design for Manufacturing Prüfung ermöglicht es uns, bei der Herstellung die Verantwortung für das Design und damit den Auftrag zu übernehmen. Hier sind ggf. auch mit dem Kunden abzusprechende Änderungen an Daten oder Design vorzunehmen, damit die erforderlichen minimalen Distanzen und andere Bedingungen erfüllt werden können.
Die Entstehung der Struktur auf den Schichten der Leiterplatten
Das Substrat für die Leiterplatte muss zugeschnitten und im Ofen präpariert werden, damit es eine ausreichende Härte erlangt und der Kunststoff später keine schädlichen Ausdünstungen von sich gibt. Anschließend werden, gesteuert durch die Daten der Software, Folien erzeugt. Jede Seite der Platine und jede einzelne Lage benötigt eine eigene Folie, auf die beidseitig in Weiß und Schwarz Farben das Grundmuster der leitenden und nichtleitenden Strukturen abgebildet wird. Die Struktur wird auf einem hoch präzisen Plotter gedruckt.
Im Anschluss werden die Folien auf hauchdünne Schichten aus Kupfer aufgebracht und mit einer zusätzlichen Schicht aus dem sogenannten Fotolack überzogen. Das ist eine chemische Verbindung, die unter dem Einfluss von UV-Licht aushärtet. Da die schwarzgefärbten Strukturen das UV-Licht absorbieren, härtet der Fotolack auf den darunter liegenden Leiterbahnen nicht aus. Mit dem Abwaschen der Folien in einer alkalischen Lösung wird die Chemikalie entfernt und es verbleibt nach der Trocknung die leitfähige Struktur aus Kupfer, während der andere Teil der Struktur nicht leitfähig ist. Dieser Prozess wird für alle Folien aller Layer der Platine wiederholt.
Ausrichtung, Qualitätssicherung und Druck
Der Prozess zur präzisen Ausrichtung aller Layer und der dazugehörigen Folien für die PCB verlangt äußerste Präzision. Nach der maschinellen Ausrichtung der Folien werden in der sogenannten optischen Stanze per Laser oder mit dem mechanischen Bohrer winzige Löcher durch die Schichten gebohrt, durch die die Schichten aneinander gestanzt werden.
Mit der optischen Kontrolle übernimmt ein Laser die Abtastung aller Schichten und den Vergleich mit der geplanten und berechneten Struktur, um mögliche fehlerhafte Verbindungen aufzudecken. Sobald die Schichten fest miteinander verbunden sind, müssen sie mit dem Substrat verklebt werden, damit die Leiterplatte schlussendlich per heißem Druckverfahren laminiert werden kann. Dabei verschmelzen Substrat und äußeres Epoxidharz oder Polyimid und bilden eine untrennbare Einheit.
Die Bestückung der Leiterplatten
Die von der Struktur her fertige Leiterplatte muss jetzt mit den Bauteilen bestückt werden, die durch die Leitungsbahnen angesteuert werden sollen. Dabei können je nach Komplexität der Leiterplatte unterschiedliche Verfahren zur Anwendung kommen. Beim Surface-Mount-Device (SMD) Verfahren werden die elektronischen Komponenten auf die Oberfläche der Platine gelötet. Dabei lassen sich gewisse Vorteile für die Miniaturisierung erzielen. Beim SMD-Verfahren wird mit dem Reflow-Löten eine spezielle Lötpaste auf der Platine angebracht, auf der die aufgesetzten Komponenten kleben bleiben.
Im Lötofen schmilzt ein Anteil der Lötpaste und es wird mit dem enthaltenen Flussmittel die elektrische Verbindung zwischen den Leiterbahnen und den Komponenten hergestellt. Bei der Through-Hole-Technologie (THT) werden die Bauteile durch Kontaktlöcher gesteckt und dort mit den Leiterbahnen verlötet. Dabei wird gleichzeitig die vertikale Verbindung zwischen den Schichten erzeugt und eine elektrische Leitfähigkeit untereinander hergestellt. Hierbei wird das sogenannte Wellen-Löten oder das Löten von Hand eingesetzt, was zeitaufwendig und damit relativ kostenintensiv ist. Das ist jedoch bei kleinen Serien oder Prototypen nicht immer zu vermeiden.
Die Bestückung per Through-Hole
Die benötigten Löcher werden mit Hochleistungsbohrern erzeugt, die softwaregesteuert und extrem präzise arbeiten. Dabei werden unterschiedliche Arten von Löchern benötigt, die entweder
- die gesamte Leiterplatte durchdringen und zur Platzierung der Komponenten dienen
- nur die obere und untere Seite der Leiterplatten durchdringen und Verbindung herstellen
- oder nur die inneren Schichten der Leiterplatte durchdringen, um diese miteinander zu verbinden.
Dabei entsteht jedoch ein weiteres Problem. Die Löcher verlaufen ja durch Substratschichten, die ausdrücklich als nicht leitend geplant sind. Um jetzt eine Leitfähigkeit herzustellen, müssen die Löcher mit einer speziellen, nur mikrometer-starken Schicht aus Kupfer überzogen werden. In diesem Prozess wird die gesamte Platte mit einer dünnen Kupferschicht überzogen, wobei die unerwünschten Anteile mit unterschiedlich gepulstem Strom entfernt werden.
Die Fertigstellung der Leiterplatten bzw. die Bestückung im SMD-Verfahren
Damit wäre die Platine eigentlich fertig, jedoch fehlen ja immer noch die elektrischen Schaltkreise und ggf. Bauteile auf der äußeren Schicht, also der Oberfläche. Diese werden, ähnlich wie jede Folie der inneren Schichten, mit einer Schicht aus Fotolack erzeugt. Nachdem die nicht ausgehärteten Teile des Fotolacks und die Reste der Kupferschicht entfernt sind, können die äußeren Kupfer-Leitungsbahnen angelegt und geprüft werden. Falls die Platinen mit dem SMD-Verfahren hergestellt werden, erfolgt jetzt der Lötprozess, mit dem die Komponenten befestigt und aktiviert werden.
Danach wird die Platine mit der Lötmaske versehen, einem Korrosionsschutz aus Metall, der alle Schaltkreise schützt und je nach Platine die Leitfähigkeit verbessert. Der anschließend aufgetragene Lötstopplack besteht aus einem speziellen Kunststoff-Polymer. Hierbei entsteht die grüne Farbe, die die meisten Leiterplatten kennzeichnet.
Ähnlich wie der Fotolack besteht die Lötmaske aus Teilen, die von UV-Wellen durchdrungen werden und anderen Teilen, die nicht aushärten. Sobald alle nicht benötigten Teile der Lötmaske entfernt sind, können die Leiterplatten im Ofen völlig aushärten und vollständig austrocknen. Schlussendlich erhalten die Platinen im Drucker eine Kennzeichnung, die alle wichtigen ID-Merkmale und ggf. Warnhinweise enthält.
Die ganzen Produktionsschritte der Leiterplattenherstellung werden meist nicht für einzelne Platinen durchgeführt. Die Leiterplatten sind vielmehr zu ganzen Paneelen zusammengesetzt, aus denen die einzelnen Leiterplatten abschließend herausgelöst werden müssen. Selbstverständlich erfolgt vor der Auslieferung der Leiterplatten und nach bestimmten Phasen immer wieder die Qualitätssicherung.