Leiterplatten –
Material und Arten
- Der Grundaufbau der einfachen Leiterplatten
- Das Substrat als Basismaterial einer Leiterplatte
- Kupfer dient als Leiter für die elektrischen Impulse
- Die Verbindung bei PCB mit mehreren Lagen
- Die Lötmaske auf einer PCB
- Die Entwicklung der Technologie in der Forschung
- Arten von Leiterplatten
- Unterschiedlich viele PCB-Layer in einem Gerät
- Starre, flexible und semiflexible Leiterplatten
Als mittelständischer Hersteller, der sich seit vielen Jahren mit der Fertigung von Leiterplatten in der Elektronik beschäftigt, sind uns die heute und früher verwendeten Arten von Leiterplatten und das dazu eingesetzte Material natürlich von Grund auf vertraut. Vermutlich liegt es daran, dass wir uns manchmal doch sehr wundern, wie wenig in der Allgemeinheit über die Funktionen und Eigenarten der Leiterplatten bekannt ist. Das gilt noch viel mehr für die Art der Herstellung der Leiterplatten, die doch in nahezu allen Geräten stecken. Ohne eine Leiterplatte mit ihren ganz verschiedenartigen Ausprägungen würde kaum noch eines der Geräte oder eine der Maschinen funktionieren, die heute im Haushalt oder bei der Arbeit in Verwendung sind – und schon gar kein Telefon.
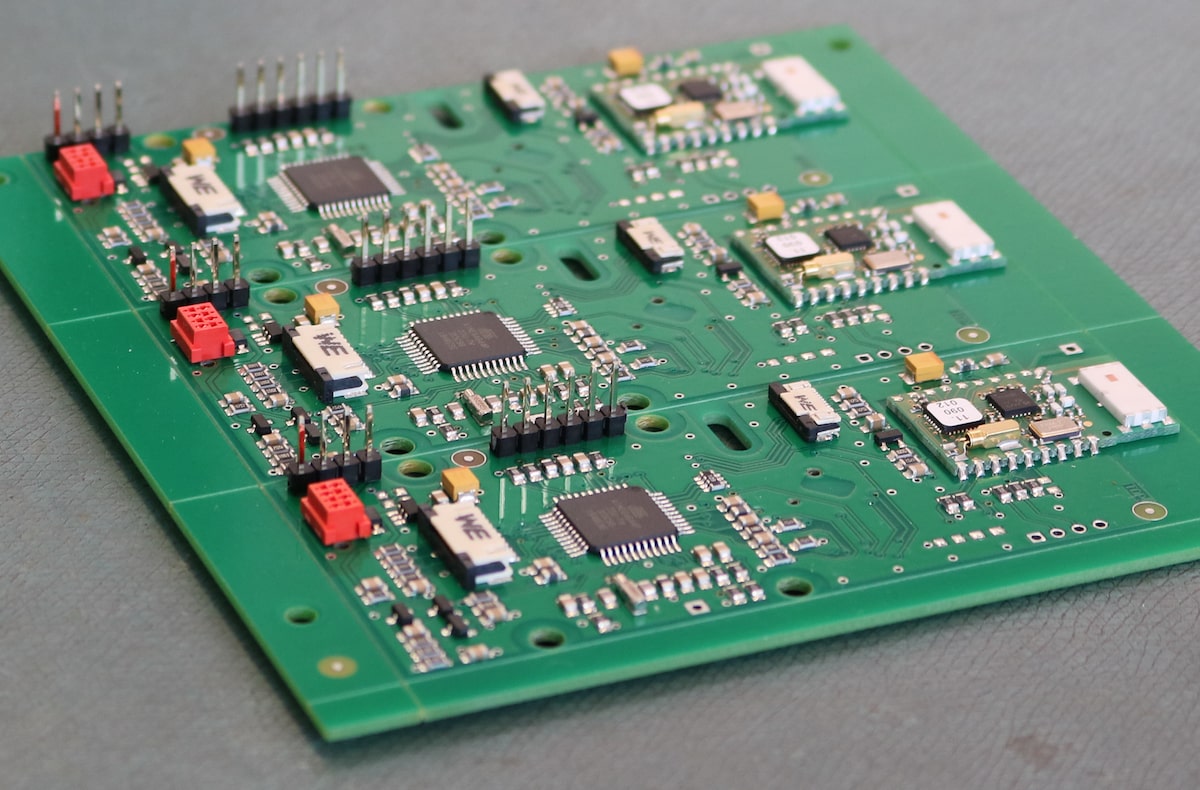
Der Grundaufbau der einfachen Leiterplatten
Die Leiterplatte wird auch Platine oder PCB genannt. Dabei steht die Abkürzung PCB für Printed Circuit Board und stellt damit eine Zusammenziehung der beiden Ausdrücke Leiterkarte und gedruckte Schaltung auf den Platinen dar. Damit haben wir schon die Funktion der Leiterkarten, PCB oder Leiterplatten und ihre Anwendung beschrieben. Die Leiterkarte dient als Träger für elektronische Schaltungen, die auf diese Karten oder eben Platinen gedruckt werden. Am Anfang jeder Produktion von Leiterplatten stehen die Daten für das Layout am Computer mit einer sogenannten Electronic Design Automation (EDA). Damit wird die Erzeugung eines Verbindungsplans und ihre Darstellung aus den Daten mit den Anforderungen der Auftraggeber ermöglicht. Der Grundaufbau der Leiterplatte selbst besteht aus zwei bis vier verschiedenen Schichten. Das sogenannte Substrat dient als eigentlicher Träger der Leiterplatten und stellt den dicksten Teil dar. Je nach Anforderung an die Leistungsfähigkeit und Komplexität der Leiterplatte besteht das einfache Substrat meistens aus einem faserverstärkten Kunststoff oder auch aus Glasfaser. Die Leistungsfähigkeit wird mit dem Wert FR4 gekennzeichnet, was auf eine größere thermische Belastbarkeit hinweist.
Das Substrat als Basismaterial einer Leiterplatte
Das heutige Substrat mit dem Wert FR4 besteht aus hauchdünnen Glasfasermatten. Sehr billige Leiterplatten werden allerdings immer noch mit durch Harz verstärktem Papier oder auch Epoxidharz unterfüttert, das allerdings häufig schnell “den Geist aufgibt”. Darüber hinaus existiert eine Vielzahl von Substrat-Materialien, die sich als Material z.B. in der Glasübergangstemperatur, der Delaminationszeit, der thermisch bedingten Zersetzung und des Ausdehnungsverhaltens in der z-Richtung der Leiterplatte unterscheiden. Alle diese Faktoren kennzeichnen die Leistungsfähigkeit und Belastbarkeit unter verschärften Bedingungen und werden z.B. mit Tests mit schnellem Temperaturwechsel geprüft. Während die günstigen Leiterplatten meistens aus einer Substratschicht mit Kupfer hergestellt werden und starr sind, existieren genauso gut Platinen bzw. PCB mit zwei oder wesentlich mehr Schichten, die umso komplexere Vorgänge schalten können. Die verschiedenen Arten Material für das Substrat werden als Basismaterial bezeichnet.
Kupfer dient als Leiter für die elektrischen Impulse
Die zweite Schicht über dem Substrat besteht aus dem leitfähigen Kupfer. Diese Schicht auf den Leiterplatten ist wesentlich dünner als das Substrat und wird ähnlich wie Papier als Menge und Stärke über das Gewicht pro Fläche definiert. Kupfer und Substrat werden als Material wie die anderen Schichten per Hitze oder Kleber miteinander verbunden. Das Kupfer soll zwar leiten, aber eben nur über bestimmte Bahnen und an bestimmten Punkten. Die Software bzw. das CAM-Programm, mit dem der Bau der Platine geplant wird, hat mit dem Layout eine genaue Vorlage erstellt, nach der das überschüssige Kupfer mit einer stark alkalischen Lösung weggeätzt wird. Dazu wird die Leiterplatte zuvor laminiert. Das Laminat besteht aus dem sogenannten Laminar, einer lichtempfindlichen Folie, die auf der Kupferschicht belichtet wird und dann als Vorlage für die Ätzspuren dient. In anderen Formen der Herstellung von Leiterplatten wird die leitende Kupferstruktur nicht durch Ätzen erzeugt, sondern bereits als Struktur auf die Platte aufgebracht. Das klingt kompliziert? Es wird noch anspruchsvoller.
Die Verbindung bei PCB mit mehreren Lagen
Je nach Komplexität der Leiterplatte kann die Beschichtung der Platte mehrfach erfolgen, sich praktisch nach innen fortsetzen und als Multilayer-Leiterplatte typischerweise 14, aber bis zu 48 verschiedene Kupferschichten und -Strukturen enthalten. Im nächsten Schritt gilt es, die verschiedenen Komponenten auf der Leiterplatte anzubringen, für die dieser komplexe Schaltkreis hergestellt wurde. Dazu werden in einem genau festgelegten Muster Bohrlöcher in den Leiterplatten angebracht, die anschließend entgratet und per Kupfer oder Kohlenstoff leitfähig gemacht werden. An diesen Löchern werden jetzt Transistoren, LEDs und Kondensatoren angelötet. Bei mehrschichtigen Leiterplatten werden zusätzliche Löcher, die sogenannten Vias, in das Material gebohrt, die die gewünschten Verbindungen zwischen den Schichten herstellen sollen. Dazu werden z.B. CO2 Laser oder UV Laser eingesetzt. Je nach Empfindlichkeit und Bedeutung der Kupferschicht und weiterer Komponenten werden jetzt z.B. Gold oder Nickel in hauchdünnen Schichten aufgetragen, um die Korrosion zu verhindern.
Die Lötmaske auf einer PCB
Zu fast jedem Schritt im ganzen Prozess gibt es Prüfverfahren und Messtechniken, die eventuelle Fehler, Lötbrücken oder tote Schaltkreise auf den Leiterplatten aufspüren. Bei der einfachen einseitigen Leiterplatte wie auf den komplexen Leiterplatten wird zum Schluss auf die Kupferstruktur eine sogenannte Lötmaske aufgetragen. Diese Schicht wird auch Lötstoppmaske genannt. Sie besteht z.B. aus lackähnlichem Polymer und soll die Oxidation der Kupferschicht verhindern, damit sich keine Lötbrücken als unerwünschte Kontakte bilden. Des Weiteren dient der Lötstopplack zum Schutz vor mechanischer Beschädigung und zur Verbesserung der Durchschlagfestigkeit. Auf die Lötmaske wird oft noch ein Siebdruck aufgebracht, der zwar keine Funktion besitzt, oft aber wichtige Informationen zur Leiterplatte enthält. Bei manuell verarbeiteten Leiterplatten wird hier auch die Platzierung von weiteren Komponenten dargestellt. Als letzter Schritt wird die fertige Leiterplatte von allen überflüssigen und überstehenden Teilen befreit und kann in die endgültige Prüfung gehen.
Die Entwicklung der Technologie in der Forschung
Schon nach dieser kurzen und sehr schematischen Darstellung kann man sehen, dass die Herstellung von Leiterplatten ein hochkomplexes Thema mit vielen verschiedenen Techniken und Methoden darstellt. Das typische Leiterplatten Material existiert genauso wenig wie der eine typische Weg zur Herstellung. Doch mag diese Übersicht genügen, um die am meisten gebräuchlichen verschiedenen Arten der Leiterplatten kurz zu beschreiben. Tatsächlich kann sich bei manchen Varianten eine ganz andere Reihenfolge der verschiedenen Schritte ergeben. Wie schon gesagt, werden für die meisten einfachen Geräte heute noch die einseitigen Leiterplatten verwendet, die als starre Gebilde billig und schnell zu produzieren sind. Aber die fortschreitende Miniaturisierung der Geräte erforderte in den letzten 50 Jahren eine große Zahl von innovativen Verbesserungen der Technik in der Herstellung. Die Vielschichtigkeit der heutigen Anforderungen für das breite Publikum findet ihren Höhepunkt in den hochwertigen Smartphones, die buchstäblich in jedem Gerät wesentlich mehr Leistungsfähigkeit, Speicherplatz und Komplexität abbilden können als in der gesamten Elektronik für die erste Mondlandung.
Arten von Leiterplatten
Folgende Arten von Leiterplatten und Materialien werden heute oft hergestellt und verwendet. Daneben gibt es noch eine ganze Reihe von Spezialprodukten, die jedoch nur anfallsweise zur Verwendung kommen.
Einseitige, doppelseitige und mehrlagige Leiterplatten
Die Technologie des Auflötens von Bauteilen, die als Surface Mounted Devices (SMD) schon in den 80er Jahren entwickelt wurden, ermöglicht zusammen mit der Through Hole Technology (THT) die Herstellung von einseitigen und doppelseitigen Leiterplatten bzw. Platinen nach den Layout-Vorgaben. Die THT ermöglicht die Verbindung zwischen den Leiterbahnen der Seiten durch die o.a. Vias. Das Layout dafür liegt bei der modernen Produktion nicht nur als berechnete bildliche Darstellung vor, sondern wird z.B. auch als Lötvorlage oder Ätzvorlage eingesetzt. Bei den doppelseitigen Leiterplatten werden nach der Erstellung der Kupfer-Struktur auf beiden Seiten zunächst die SMD-Bauteile per Wellenlötanlage oder Reflow-Löten auf die Leiterbahnen angelötet. Je nach Eignung und Zweck der Platinen wird dabei sogar manuell gelötet. Zur besseren Ausnutzung der Platzverhältnisse sind daraufhin die sogenannten Multilayer-Leiterplatten entwickelt worden. Hierbei werden, wie gesagt, bis zu 48 extrem dünne Platinen mit vorher imprägnierten Fasern aufeinander geklebt.
Multilayer-Leiterplatten / Platine
Bei der Multilayer-Platine verfügt jede der Ebenen über eine eigene Schicht Substrat. Dazu war seinerzeit auch die Weiterentwicklung des Basismaterials und seiner Fähigkeiten nötig. In dieser Zeit der 90er Jahre begann daher die Temperaturbeständigkeit z.B. im Bereich des FR4 eine große Rolle zu spielen. Die Entwicklung doppel- oder mehrlagiger Platinen hat jedoch keinesfalls zum Verzicht auf die jeweils früher gebräuchlichen Leiterplatten geführt. Einseitige, doppelseitige oder Multilayer-Leiterplatten werden nach wie vor eingesetzt. Auch mit der modernsten Technologie sind die einseitigen Leiterplatten heute immer noch am günstigsten in der Herstellung. Oft finden sich alle drei Versionen der Platinen in ein und demselben Gerät und seiner Elektronik. Die Multilayer-Leiterplatten stellen die Hersteller immer noch vor die größten Herausforderungen. Das betrifft vor allem die Prüfläufe, denn ein winziger Fehler auf einer der vielen Schichten mit ihrem Basismaterial kann die gesamte Konstruktion ruinieren. Große Sprünge werden auch heute noch in der Weiterentwicklung der Materialien gemacht.
Starre, flexible und semiflexible Leiterplatten
Je nach Basismaterial und Beschichtung haben die PCB, also Platinen, heute eine ganz unterschiedliche Konsistenz. Die seit jeher bekannten starren und stabil wirkenden Leiterplatten bauen auf ein Substrat aus Glasfaser und/oder Harz auf. Doch sie sind anfällig für Bruch unter Belastung und eignen sich nicht für die Elektronik in gebogenen Geräten. Das Substrat und das Basismaterial für flexible Leiterplatten erlaubt auf Basis von Polyimid-Folien die Herstellung von ganzen Leiterfolien. Diese sind zwar teuer in der Entwicklung und Produktion, aber zeigen sich stabil und belastbar. Manchmal sieht man sie bei einem Vierfarb-Drucker in Betrieb. Die semiflexiblen oder starrflexiblen Leiterplatten verbinden beide Eigenschaften der Biegsamkeit und der Starrheit. Diese Platinen bestehen aus einem jeweils unterschiedlichen Substrat und sind durch Löcher bzw. Vias miteinander verbunden. Unter den Spezialplatinen lassen sich noch die Hochfrequenz-Leiterplatten und die Aluminium-Leiterplatten erwähnen. Erstere sind für Frequenzen ab 500 MHz entwickelt worden, bei denen sich eine große Störanfälligkeit ergibt. Sie bestehen z.B. aus den Materialien Epoxy-Laminat im FR4 Bereich, PPO-Harz und Teflon. Sie müssen besonders geerdet werden. Die Aluminium-Leiterplatten werden für die Elektronik bei hohen mechanischen und thermischen Belastungen eingesetzt, wobei das Aluminium selbst als Wärmeableiter fungiert.